Technology For Pneumatic Conveying System
- What is a Pneumatic Conveying System?
A pneumatic conveying system moves dry bulk materials or powders through an enclosed pipeline. It uses air pressure created by devices like fans, blowers, or compressors, to transport the materials.
Pneumatic conveying offers an economical solution for efficiently transporting powdered and bulk granular materials with minimal loss. It’s ideal for various industries, including Food and Beverage, Pet Food, Chemicals and Detergents, Renewables, and Specialty Materials.
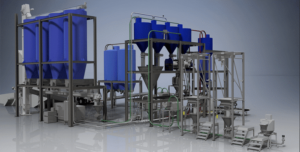
A pneumatic conveying system is excellent for preventing product contamination. This is because the system uses enclosed pipelines to transport materials.
Since the materials are moved through sealed tubes, they are protected from external contaminants like dust, dirt, and other impurities. This makes pneumatic conveying ideal for industries that require high levels of cleanliness and hygiene, such as food processing, pharmaceuticals, and chemicals.
Additionally, the enclosed nature of the system minimizes the risk of cross-contamination between different batches of materials. This ensures that the quality and purity of the products are maintained throughout the conveying process.
Overall, pneumatic conveying systems provide a clean, safe, and efficient way to handle and transport materials while preventing contamination.
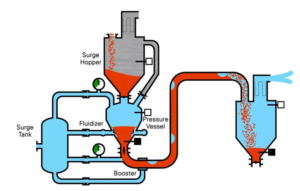
2. Pneumatic Conveying Is Divided into 2 Main Categories
• Dense Phase: This method uses low-velocity air to move materials in a more compact form. It’s ideal for heavier, abrasive materials and helps minimise wear and tear on the system.
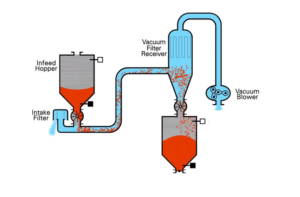
• Dilute Phase: This method uses high-velocity air to transport materials through the pipeline. It’s suitable for moving lighter, non-abrasive materials over long distances.
3. Pneumatic Conveying Systems Offer Several Advantages
• Low Maintenance: With fewer moving parts compared to mechanical systems, pneumatic conveyors typically require less maintenance.
• Increased Safety: The reduced number of moving parts also means there’s less risk of injury to operators and maintenance workers.
• Minimal Dust and Spillage: Since materials are transported through enclosed pipelines, there’s less dust leakage and spillage, leading to a cleaner and safer work environment.
• Better Sanitation: The enclosed nature of the system reduces the risk of contamination, making it ideal for industries like food and pharmaceuticals.
• Flexibility: Pneumatic systems can be custom-designed to fit around existing equipment and can handle multiple infeed and destination points, as well as longer conveying distances.
4. Disadvantages of Pneumatic Conveying:
• Pneumatic systems use air pressure to move materials, which makes them less efficient than mechanical conveyors.
• They are usually used for moving smaller amounts of materials. While they can handle larger volumes, it can be more challenging.
• Since dust needs to be removed at the end of the system, a bigger dust collection system might be required.
• Heavy materials, that have large particles, sticky or wet materials may not work well with pneumatic conveying.
5. Vacuum vs Pressure
A vacuum system draws materials through the pipeline and is well-suited for pressure-sensitive, non-abrasive materials. In contrast, a pressure system pushes materials through the pipeline and can handle abrasive substances. For example, quartz and copper sulfate are types of abrasive materials that a pressure system can effectively transport.
Non-abrasive powders, such as moringa powder and powdered metals, are effectively conveyed using a vacuum pneumatic conveying system.
6. When evaluating your application, consider the following factors
• Particle Size and Shape: The size and shape of the particles can affect how they move through the system.• Air Humidity: The moisture in the air can impact the conveying process.
• Moisture Content: The amount of moisture in the materials can influence flow and handling.
• Flow Angles: The angles of flow, slip, and repose determine how materials settle and move.
• Density: The density of the materials affects their behaviour in the system.
• Fluidization: How easily materials can be fluidized impacts their conveyance.
• Hardness/Friability: The hardness or tendency of materials to break apart can affect system wear and performance.
• Temperature: The temperature of the materials and environment can influence the process.
• Concentration: The concentration of materials in the air stream is crucial for efficient conveying.
• System Throughput: The amount of material the system can handle over time.
• System Distance: The distance materials need to be conveyed affects system design and efficiency.
These factors help to ensure your pneumatic conveying system is designed for optimal performance.
7. Differences Between Dense Phase And Dilute Phase In Pneumatic Conveying
There are several differences between dense phase and lean phase pneumatic conveying. Some differences are due to the nature of the materials being moved. For example, lean phase (dilute phase) conveying often handles lighter particles. Other differences are necessary to ensure the materials are handled properly and to prevent issues like abrasion or breaking down of particles.
• Velocity: The velocity in dilute phase pneumatic conveying systems is usually faster compared to the dense phase, typically ranging between 700 and 1,000 m/min. The velocity of dense phase conveying is only about 200 m/min, given how abrasive the particles being carried are.
• Air pressure: The air pressure inside air ducts, tubes, and pipes of a dilute phase conveying system is relatively low compared to either lean phase conveying or dense phase pneumatic conveying. While the dilute phase has air pressure of less than 100 kPa, the dense phase has air pressure of 100kPa up to 600kPa.
• Attrition: Attrition means the breaking down of powder. In a dilute phase system, attrition can be very high because the particles move quickly.
• In dense phase pneumatic conveying, it’s the opposite. The materials move at lower speeds, so they are less likely to break down into powder.
• Pipe Size: In dilute phase conveying systems, the pipes are usually larger compared to those in dense phase systems. The components used in these systems also differ slightly in their specifications. This is because the best performance depends on the type of particles being transported and how abrasive or sensitive they are.
• Expertise: Dense phase conveying needs a higher level of expertise. Engineers working with dense phase systems must have more specialized knowledge compared to those working with dilute phase systems. This is because dense phase systems are more complex and require careful handling to ensure proper operation.
• Cost: Building a dense phase conveying system is usually more expensive because the components are more heavy-duty compared to those in a dilute phase system. Additionally, dense phase conveying is still relatively new, so there are fewer vendors available. This means fewer options for repairs, and you might need to go back to the original designer or engineer for support if there are issues.
• Loading Capacity Or Ratio: Dilute phase pneumatic conveying systems have a low solid-to-gas mass loading ratio of up to 15. In comparison, a dense phase system has a very high solid-to-gas mass loading ratio of 100 or more.
• Distance: The maximum distance for conveying materials differs between the two systems. A dilute phase system can transport materials up to the max. 200 meters, while a dense phase system usually handles distances of less than 100 meters.